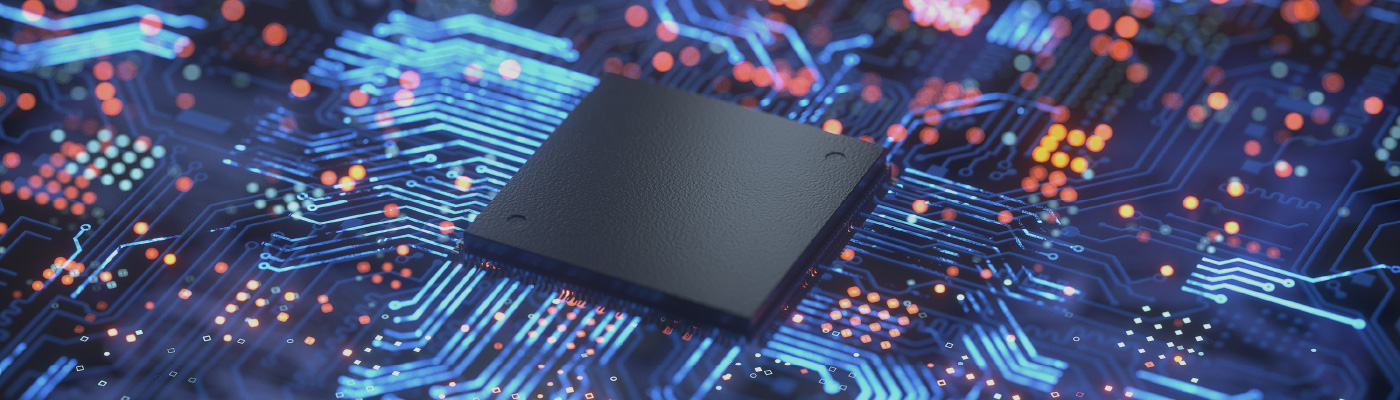
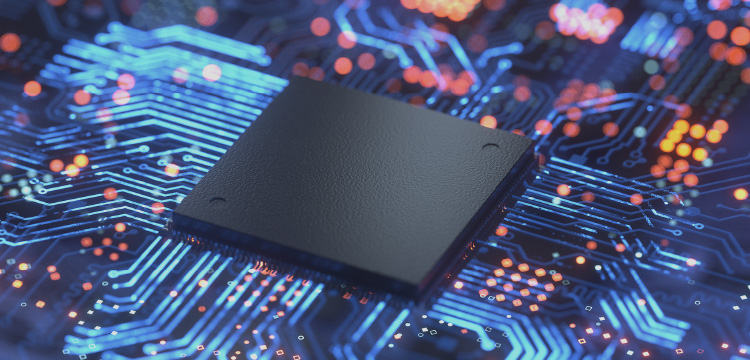
PROCESS
半導体の製造工程
開発工程
-
開発テーマ決定
「まだ世の中にないもの」を作るため、デバイス開発エンジニア、基盤技術開発エンジニア、プロセス技術開発エンジニアが必要な要件を話し合う。クライアントからの要望を叶える開発、今後こういう性能が求められるだろうというデバイスを実現するためにエンジニア同士で話し合って進める開発、両方を考慮して進めていく。
-
より性能を上げるためのデバイス構造を各エンジニアが話し合って決めるよ!
-
担当する場所が違うようで、この段階では3つの部署のエンジニアが重なり合った役割をこなすんだ。
-
特殊機能を実現するための
デバイス構造の検討、開発特殊なある機能を実現するためのデバイスを考案する場合、回路の設計だけではなく、デバイス構造そのものも考えなくてはならない。さらに、性能を上げるためのトランジスタの構造も同時に開発する。
-
プロセス設計
新しいものを作るためには、あらゆる選択肢を考慮して、ものすごい量の組み合わせのパターンを検証する必要がある。そのため量産工程(前工程)の③〜⑨の順番のパターンを膨大な可能性の中から検討し決めていく。そして、求められる要求に対しベストな組み合わせを成り立たせていく。
-
モジュール回路設計
1〜2億個のトランジスタの組み合わせを工夫することで、一つの大規模集積回路を実現する「製品回路設計」。それをプロジェクトのたびに一から設計するのは時間がかかるため、ある特定の機能の部分だけ切りだし、先に開発する。
-
各種シミュレーション
各々の設計した要件が成り立つか検証する。さまざまな条件を組み合わせてその性能が出るかどうか、試作まですると時間も費用もかなりかかるため、シミュレーション環境で確認する。この段階で、数千の組み合わせを何十パターンまでに絞り込むことができる。
-
要素技術開発
量産工程(前工程)の①ウェハの酸化〜⑨電極・配線形成、各々の技術開発を行う。さらに各々の要素技術だけではわからない、実際にパターンを作って求めていた性能が出るかどうか等の確認も行う。要素技術開発では、短い工程での出来栄えの確認と、何十パターンもの組み合わせも行い最終の製品まで近づけていく。
-
試作・評価
想定したものが作り込めているか、試作、微調整、確認、評価をする。
素材加工過程
-
シリコンインゴットの引き上げ
半導体のベースになるシリコンの単結晶を作り、多結晶原料を溶融後、引き上げる。
-
半導体のベースとなるシリコンの単結晶棒(インゴット)。素材加工会社の技術が詰まってるんだ!
-
-
シリコンインゴット切断
シリコンインゴットを薄く切断しウェハを作る。
-
ウェハ研磨
ウェハの表面を鏡面状に研磨する。
-
ここまでの作業を終えたウェハを受け取って、いよいよTPSCoの量産加工(前加工)を始めるよ!
-
マスク製作工程
-
製品回路設計
クライアントが設計した回路をマスクパターンにする。
TPSCoが開発したモジュール回路を使用する場合は、必要に応じてその情報をクライアントに提供する。
全体の回路についてはTPSCoの回路設計ルールをベースに、クライアントが設計をする。 -
フォトマスク作成
透明なガラス板に設計した回路パターンを焼き付ける。
-
マスク製作工程を終えた状態で、量産工程(前工程)④からTPSCoが作業を始めるパターンもあるよ!
-
量産工程(前工程)
-
ウェハ表面の酸化
ウェハを高温の拡散炉の中で酸化性雰囲気にさらし、表面を酸化させる。
-
ようやく準備が整った!いよいよ量産加工(前加工)が始められるよ!
-
量産加工(前加工)は生産プロセス・設備エンジニアと品質保証エンジニアが活躍するんだ!
-
-
薄膜形成
ウェハ表面に薄膜をつける。
-
フォトレジスト塗布
フォトレジストという感光剤を含む樹脂をウェハ上に薄く均一に塗布する。
-
どの工程でも検査条件をクリアしているか、生産プロセス・設備エンジニアや品質保証エンジニアが確認!
-
-
露光・現像
レンズを通じて、ウェハ表面に回路パターンを焼き付ける。
-
担当する装置が順調に動いているか常に監視しているよ!
-
-
エッチング
部分的に薄膜を除去し回路のパターンを残す。
-
一つのウェハを作り上げるのに、例えばエッチング工程は1回やれば終わり、ではなく数十回の作業を実施するんだよ!
-
-
イオン注入
イオン注入によって不純物濃度のコントロールをして、拡散層を作る。
-
レジスト剥離・洗浄
薄膜の上に残ったレジストを剥がす。薄膜の表面が露出したら、ウェハ表面に付着している微粒なゴミを洗浄する。
-
ウェハの大きさを東京ドームの広さに例えると1mmのゴミ1つ以下に制御する、すごい技術を持っているよ!
-
-
平坦化
ウェハ表面を研磨し、パターンの凹凸を平坦化する。
-
電極・配線形成
ウェハ表面に電極配線用のアルミ金属膜を作る。チップ内部と外部を電気的に接続するための通り道に。
-
髪の毛1本の、1000分の1もの微細なものをコントロールする技術が集まっているんだ。
-
-
検査
ウェハに形成された数百〜数千のチップを試験し、良品の判定をする。
-
③〜⑨は製品要求によって複数回・複数パターンで繰り返される。24時間休みなしで稼働しても3か月はかかる大変な作業だよ。
-
-
量産工程(後工程)
-
ダイジング
ウエハを切断し、チップを切り離す。切り離されたチップは「ダイ」と呼ばれる。
-
ワイヤーボンディング
リードフレームとチップを金線、銅線等で接続する。
-
モールディング
キズや衝撃を防ぐため、セラミックやモールド樹脂などのパッケージに封入する。
-
最終検査
電気的特性検査、外観構造検査などを行い、良品の確認をする。
-
出荷
-
TPSCoのイメージセンサは医療用X線カメラや、ハリウッド映画撮影用カメラに供給されているよ。私たちのテクノロジーを使用したカメラで賞を受賞した作品もたくさん。
-
より優れた製品を生み出すために、開発テーマを決め、日々がんばっているよ。
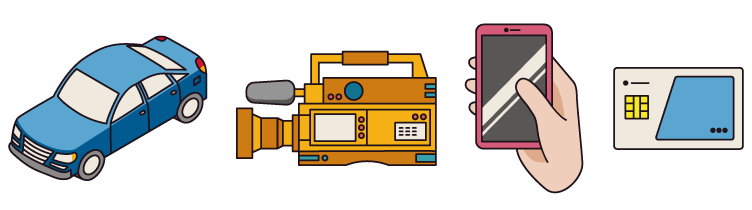
業界最先端のパワーマネジメントプラットフォームは低電力から高電力アプリケーションまで最大700Vに至る電圧範囲に対応。先進運転支援システムADASなどの多様なアプリケーション向けの実績が。今後、農業や人の移動に自動運転が活躍する時代が来たときに、私たちの技術が役に立てていたらうれしいよね。
どんな開発テーマがあるかというと、例えば、デジカメのイメージセンサ。